油壓滾牙機作為金屬螺紋加工的核心設備,其冷卻油的選擇直接影響加工精度、模具壽命及生產效率。本文結合行業實踐與材料科學原理,系統闡述油壓滾牙機冷卻油的選型要點及典型應用場景。
一、核心性能指標:構建冷卻油評價體系
1.極壓抗磨性
滾牙工藝中,模具與工件接觸區壓力可達3000MPa以上,需冷卻油具備極壓添加劑(如硫、磷、氯復合物)以形成化學吸附膜。例如,某汽車零部件企業采用含硫化極壓劑的專用滾牙油后,模具壽命從8000件提升至22000件,螺紋表面粗糙度Ra值降低40%。
2.熱傳導效率
加工過程中,局部溫升可達500℃/s,冷卻油需具備高比熱容(≥2.0kJ/kg·K)和導熱系數(≥0.15W/m·K)。實測數據顯示,使用合成酯類冷卻油可使加工區溫度較礦物油降低35%,有效抑制熱變形導致的螺紋節距誤差。
3.粘度適應性
根據加工材料調整粘度等級:
①低碳鋼:ISO VG 32-46
②不銹鋼:ISO VG 68-100
③有色金屬:ISO VG 10-22
某航空零件廠針對鈦合金滾牙,選用粘度指數(VI)>150的全合成油,在-20℃至150℃溫區內保持穩定潤滑膜厚度。
二、典型應用場景與油品推薦
1.黑色金屬加工
碳鋼、合金鋼等材料推薦使用含氯化石蠟的極壓型冷卻油。例如,DP低油霧滾齒機切削油通過非離子表面活性劑技術,實現工件表面殘留油膜厚度≤0.5μm,滿足后續電鍍工藝要求。
2.不銹鋼精密加工
304/316不銹鋼需采用生物降解型合成油,其極壓添加劑采用有機鉬化合物,既保證潤滑性又符合ROHS環保標準。某醫療器械企業應用后,產品表面鎳層附著力提升2個等級。
3.有色金屬擠壓
鋁、銅等軟金屬加工建議使用白礦油基礎油,配合脂肪酸酯潤滑劑。某電子連接器廠商采用該方案后,滾壓毛刺高度從0.03mm降至0.008mm,產品合格率提升至99.7%。
三、工藝優化實踐:冷卻油與設備參數聯動
1.油溫控制
通過板式換熱器將油溫維持在40-60℃區間,可使冷卻油粘度波動范圍縮小至±5%,確保潤滑膜厚度穩定性。某重工企業采用該措施后,滾牙機主軸振動值降低62%。
2.噴淋系統改造
采用高壓霧化噴嘴(壓力≥0.7MPa)配合低粘度冷卻油,可使油霧顆粒直徑≤50μm,滲透性提升3倍。某軸承制造商改造后,滾壓輪單次修磨周期延長至1200小時。
3.油品壽命管理
建立酸值(TAN)監測體系,當酸值>1.5mgKOH/g時立即更換油品。某能源企業通過該措施,將冷卻油更換周期從3個月延長至9個月,年節約成本48萬元。
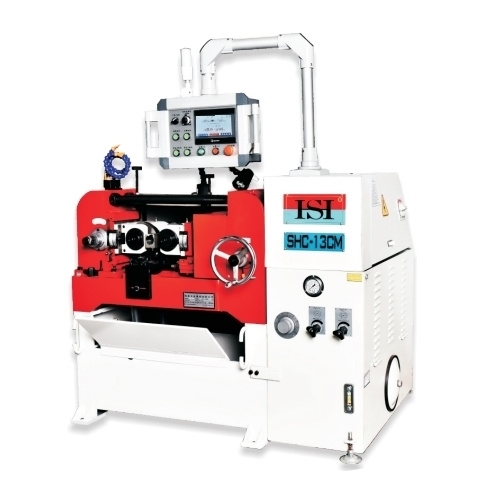
四、未來趨勢:智能化冷卻系統
新一代油壓滾牙機正集成物聯網技術,通過在冷卻油中嵌入納米傳感器,實時監測:
1.極壓添加劑濃度(電化學阻抗譜法)
2.金屬磨粒含量(磁性塞檢測)
3.氧化程度(紅外光譜分析)
某智能工廠試點項目顯示,該系統可提前72小時預測油品失效,使非計劃停機時間減少85%。隨著數字孿生技術的深入應用,冷卻油選型將從經驗驅動轉向數據驅動,推動金屬加工行業向零問題制造邁進。