三軸滾牙機作為管螺紋加工的核心設備,憑借其等邊三角形滾壓原理和液壓驅動系統,在汽摩配件、冷凝器銅管等領域廣泛應用。然而,要實現高精度、高效率的加工效果,操作技巧與安全規范缺一不可。
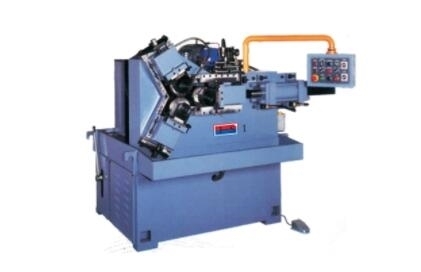
1.精準調距:構建等邊三角形的黃金法則
設備調試是滾牙加工的第一道關卡。以加工空調蒸發器銅管為例,需先將三個滾絲輪安裝至支撐軸,通過調整活動導軌使輪間距形成等邊三角形。實際操作中,可用色筆在工件表面標記,手動轉動皮帶輪觀察牙印銜接情況。若出現錯位,需以任一滾輪為基準,松開其余兩輪的連軸器,通過刻度盤微調至牙印完整閉合。某汽配廠案例顯示,未嚴格遵循等邊三角形原則導致廢品率高達15%,而規范操作后合格率提升至99.2%。
2.動態對牙:分步滾壓的精細控制
滾壓過程分為半牙與全牙兩個階段。半牙階段需控制液壓壓力在35kg/s以下,邊滾壓邊調節油缸行程,通過多次試壓確保螺紋深度達標。全牙階段則需松開軸承座壓緊螺母,調整主軸角度至接近螺紋升角,再重復半牙工藝。某精密制造企業采用"三段式滾壓法":首段低速試滾確認牙型,中段提速至80r/min保證效率,末段減速檢查表面光潔度,使單件加工時間縮短40%。
3.安全防護:人機協同的雙重保障
操作前必須穿戴防護眼鏡、防切割手套等裝備,并檢查接地裝置是否可靠。加工過程中嚴禁手伸入滾輪區域,調整牙位時需先切斷電源。某機械廠事故分析表明,70%的工傷源于違規操作,如未停機清理鐵屑導致手指卷入。此外,設備需每日清理冷卻液箱,每月更換減速器潤滑油,每季度檢查液壓系統密封性,這些維護措施可使設備壽命延長3-5年。
4.效率優化:參數匹配的智能決策
針對不同材質需動態調整參數:加工鋁合金管時,切削速度可提升至120m/min,進給量控制在0.15mm/r;而不銹鋼件則需將速度降至60m/min,進給量減至0.08mm/r。某新能源企業通過安裝智能傳感器,實時監測主軸負載,當壓力超過額定值80%時自動降速,使設備故障率下降62%。
從等邊三角形的幾何校準到液壓參數的智能調控,三軸滾牙機的操作既是技術活更是精細活。掌握這些核心技巧,不僅能提升加工精度,更能構建起人機協同的安全屏障,讓這臺精密設備在工業生產中持續釋放價值。